Project Overview:
Sheila & John Fassler were experienced in treating childrens head lice as owners of Pediatric Hair Solutions but their experience recognized shortcomings of their existing hardware. They partnered with Caliber to create a lice treatment which delivered a quieter, more effective, and more modern experience to their clients.
Benchmarking/Project Outline:
As with most new projects, the process began with research, benchmarking of existing technology, and review of the many solutions presently on the market. Following that we started by keeping it simple. The very first prototype was reduced to a blower, a heater, and a single simple regulator circuit. This “simple first” design approach using primarily off the shelf parts and materials led to a basic low cost solution with good performance. In this version, an expanded PVC tube was utlized to help attenuate sound while a structured accoustic pathway was engineered to allow airflow while further reducing sound using accoustic foam internally.
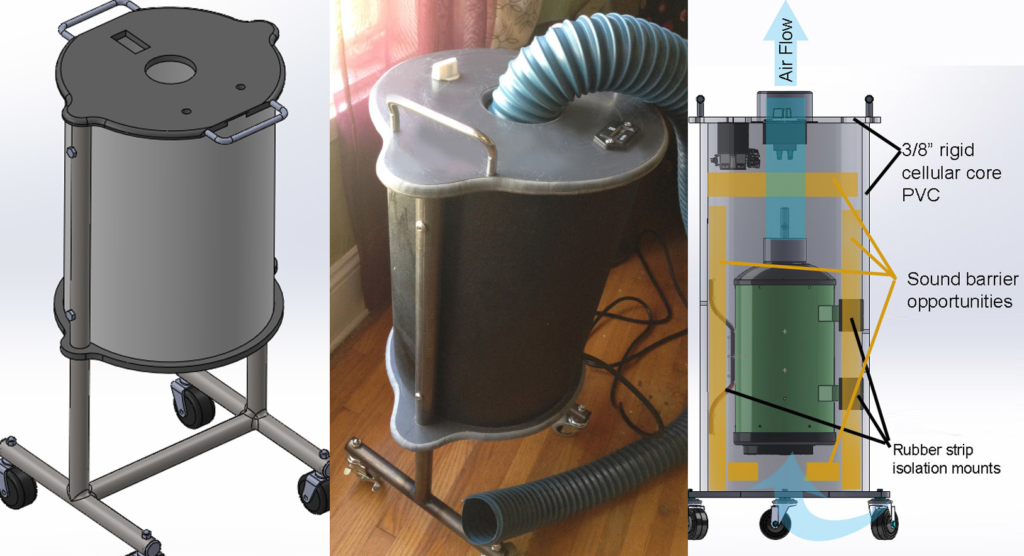
“Works-Like”/Proof of concept:
This intial prototype set the path for the design language moving foward. While the system did work as intended, the design specification established early on called for a solution with greater reliability and consistency.
“Looks-like/Works-like”:
A new prototype was created which utilized a microcontroller to continuously monitor temperature and solid state components to regulate flow and implement additional user conveniences including visual, timing, and user interface features. Use of a specialized hose component allowed for a remote illumination circuit to seamlessly deliver power to the hose end while eliminating the unwieldly use of a free floating wire within the air delivery tube. This further enabled the tube to collapse along its axis and the enclosure allowed for stowage and protection entirely inside the PVC shell. The original welded tube frame rolling chassis was simplified to an extension of the cylindrical shell to simplify constuction and allow for stowage volume. A more sophisticated electronics package was then designed, programmed, and implemented.
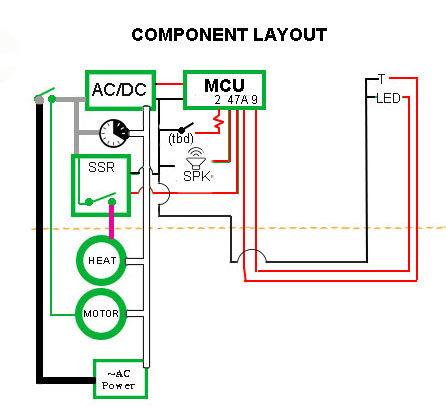
Concept Refinement:
Following these innovations, we turned to the blower head for refinement. A contoured, replaceable, solution was developed which was:
- Contoured:-the base enclosure matched the general geometry of a patient’s scalp.
- Transparent- the clear material allowed for light to pass through for scalp inspection during and after treatment.
- Removeable & Reusable-A novel sliding nozzle assembly allowed for easy cleaning and sterilization while parallel side rails and magnetic latch provided a fast, reliable air seal and easy maintenance.
- Telescoping-while the intial contour was established by the base, each additional exhaust cone was keyed and static air pressure was utilized to help extend the cones to exactly match the patient’s scalp. By allowing the heated air to flow at closer range to the scalp, a faster, more effective procedure was implemented and because the diversion tips contact the scalp surface there was no compromise to user comfort.
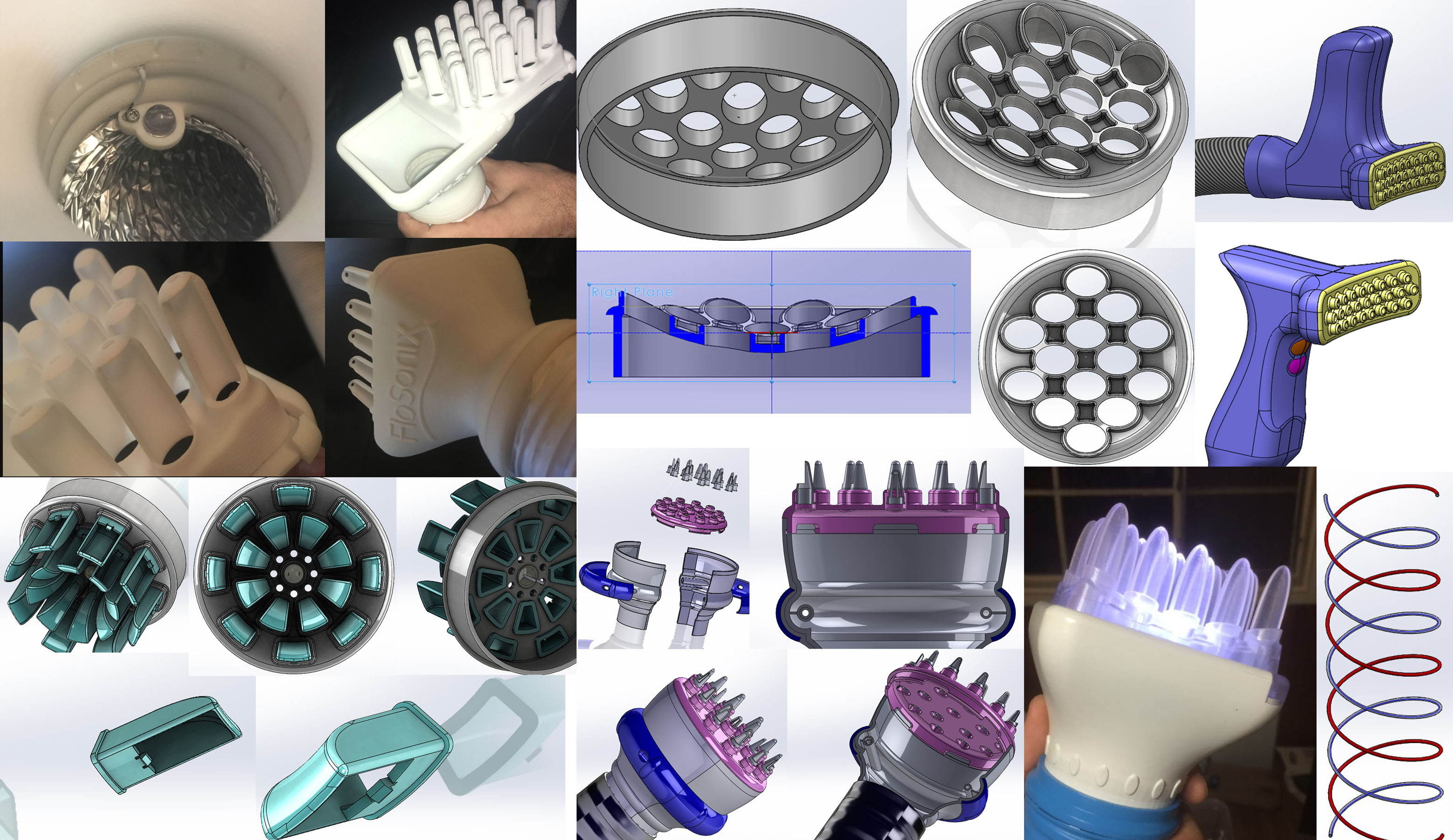
Development:
During the head development several test rigs were created to evaluate performance. These rigs included sensors to monitor temperature and flow as well as a thermal (infrared) camera to assess temperature overall and specific heating patterns associated with changes to the head design. A transparent model head was created to include both simulated hair and hydrochromic dessicant beads to document the dehydration pattern, time, and effectiveness. Measurements of pressure, flow, and illuminations were also documented at this time.
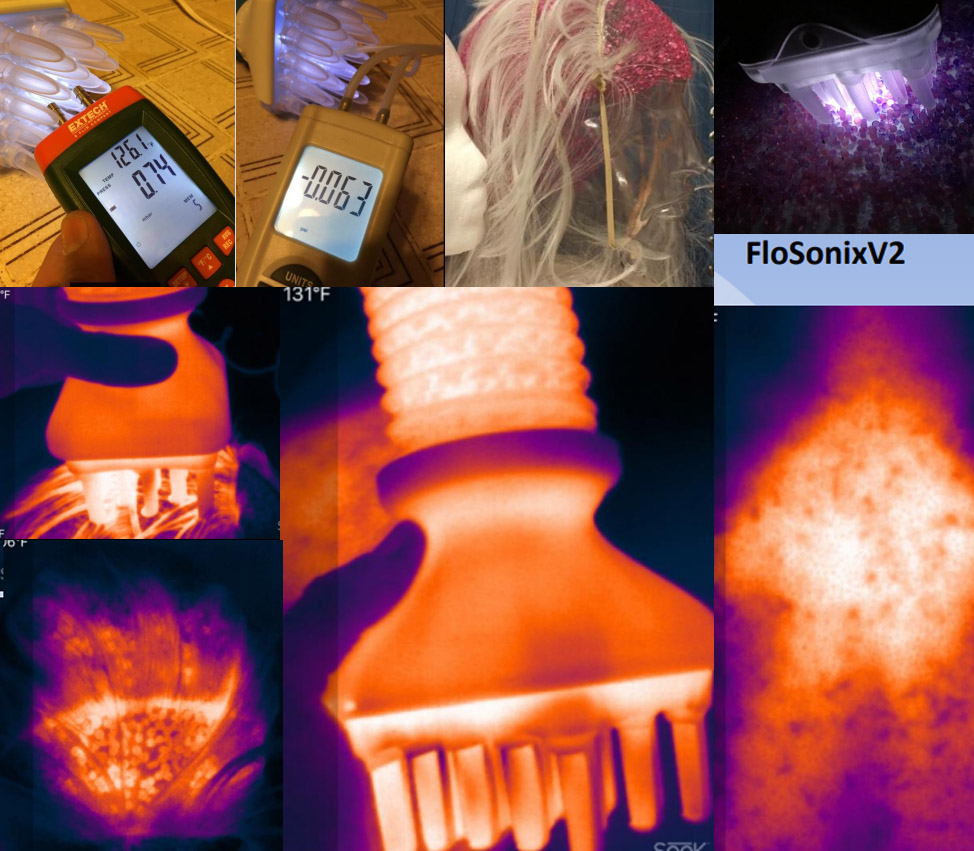
All of these resources were continuously utilized to refine the design and implement innovation as progress continued.
Final Prototyping:
Following successful validation and solidification of target goals more than 20 prototypes were generated in house for reliability testing and further validation. Base materials were constructed from readility available PVC components and fabricated in our shop. Material was evaluated, validated, and finally optimized for limited local production using a waterjet cutting process and hand assembly.
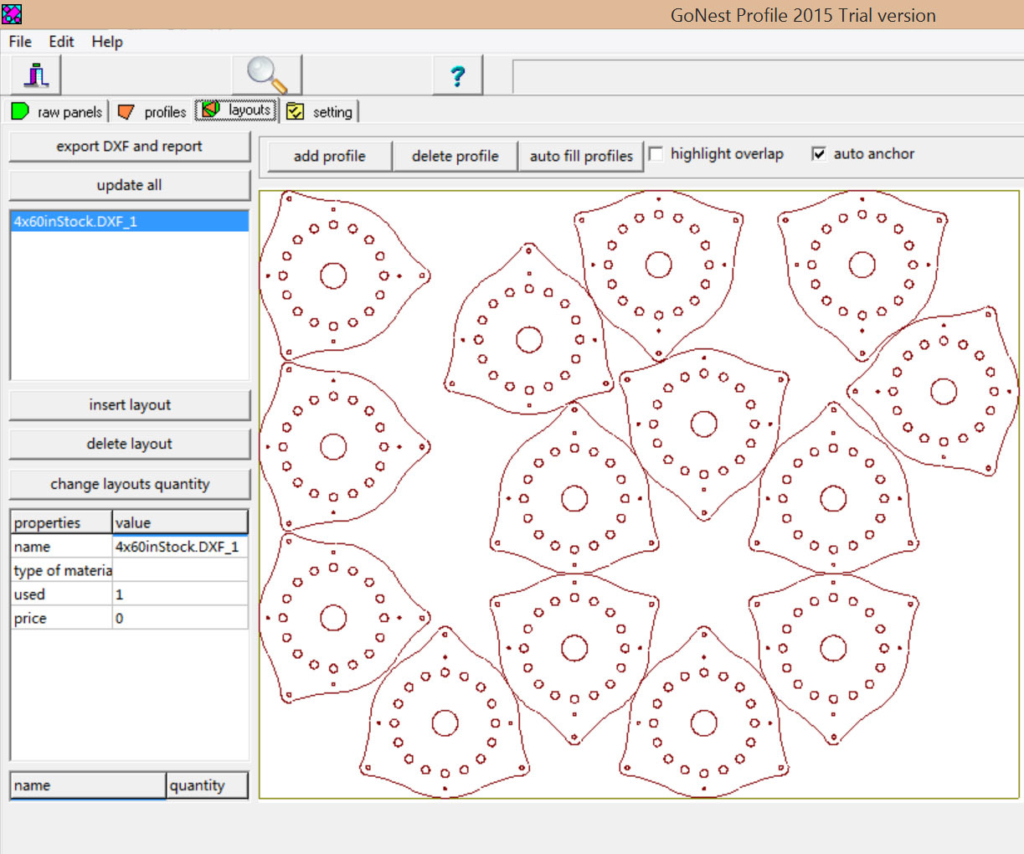
Software was refined for maximum performance and reliability and audio cues were adjusted for maximum user clarity. Preliminary sourcing was initiated and arrangements with factories overseas was begun. Simultaneously, graphic design and marketing decisions were being made and partners were brought in to help. Preliminary decals were used to begin to build our branding foundation.
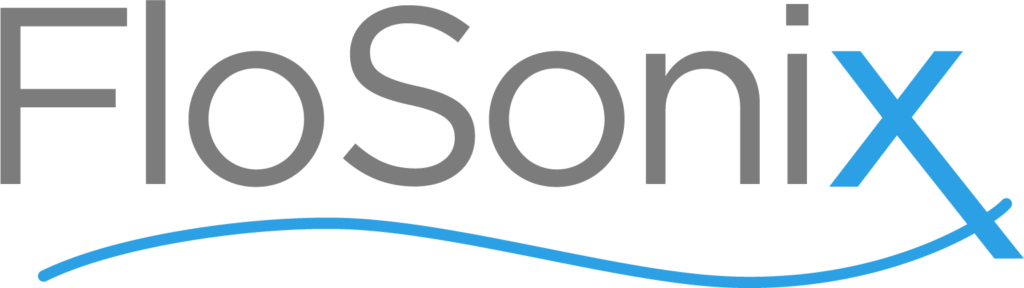
Design For Manufacture (DFM):
Our client’s desire to combine domestic (local) manufacturing with sourced components to help with certificaiton and reduce costs resulted in a trip to Asia to meet with vendors in Shanghai/Ningbo, Shenzhen & Hong Kong. This trip allowed for an in person discussion of appropriate hardware and customized solutions and included a stop with a vendor interested in repurposing their heating device intially intended for veterinary surgery.
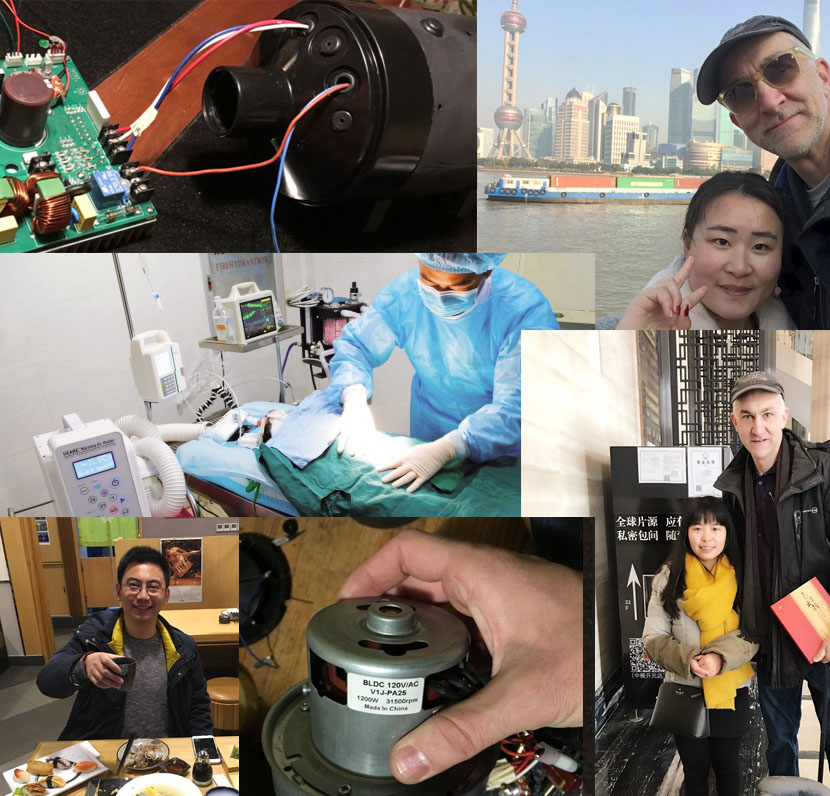
Another vendor was able to customize and supply a lightweight hose with the unique properties of high flexiblity, collapsability, and a structural wire which also served as an electrical ground. Ongoing correspondence with manufacturers based in China led to development of a customized solution.
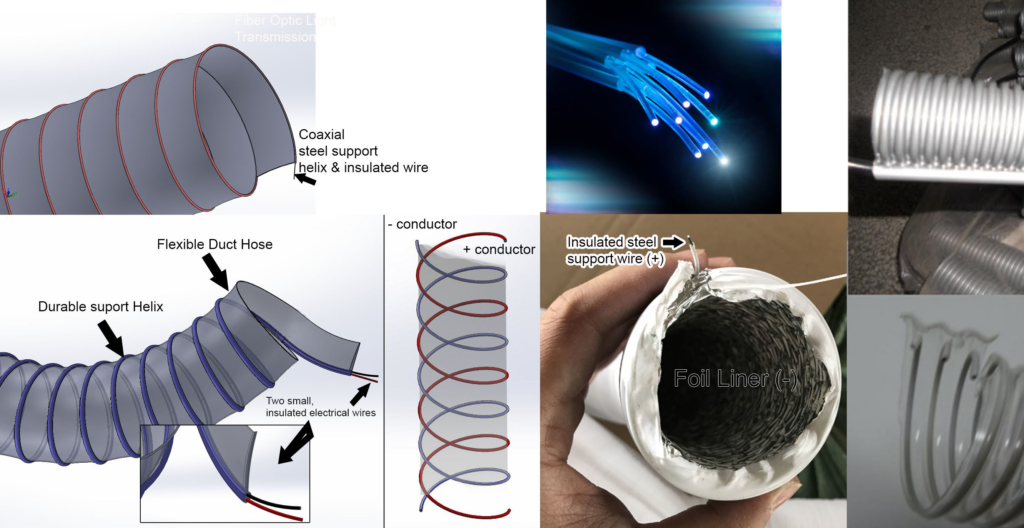
Following this trip more refinement was rendered and a local partner was brought in to add software features such as cellular connectivity, and security and also to establish a continuous larger volume production capability. A brushless motor was implemented to improve efficiency while elimnating the need to replace brushes.
Handoff/Support & Partner collaborations.
Final refinements to the product design were delivered along with a collection of external parters for final manufacturing, delivery and service. Support for this successful program is ongoing as needed and requested.
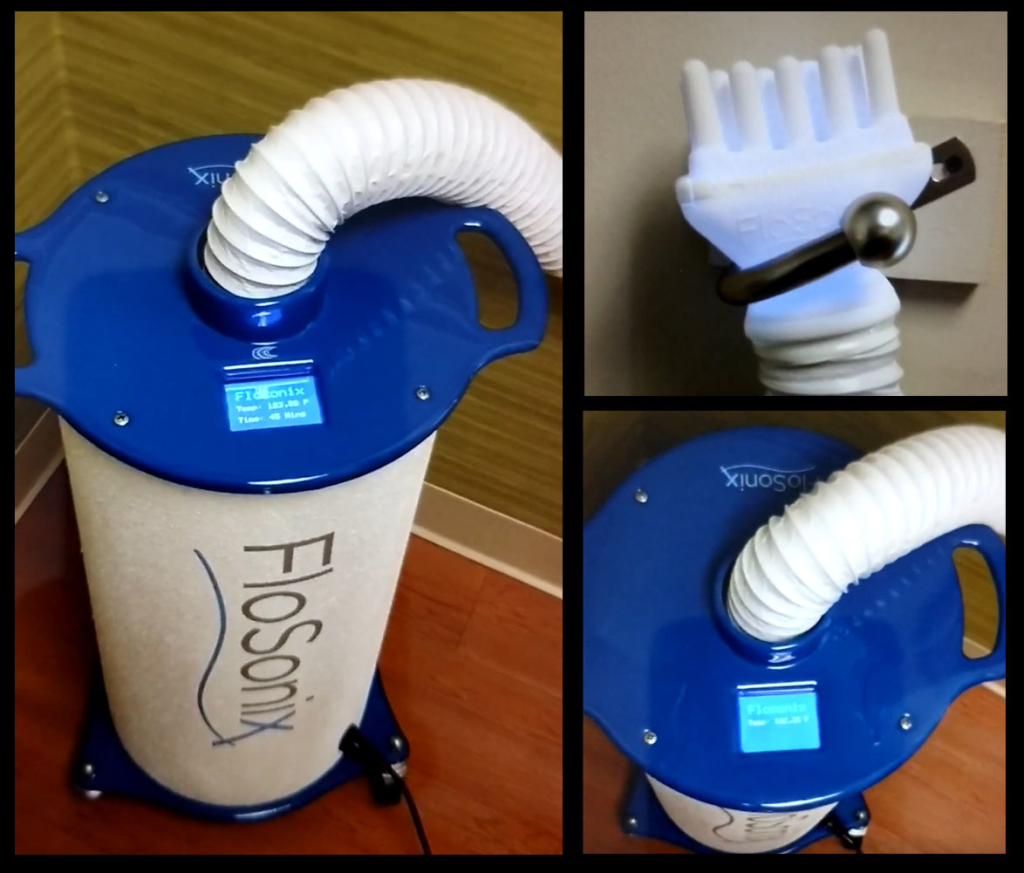
For the latest revision, updates and present design please visit http://www.flosonix.com