“Kevin’s work was critical in the initial stages of prototyping and developing my invention, and it formed the foundation of what it’s turned into today.”-Dr. Grant Coleman
Dr. Grant Coleman had been moving teeth for years the old fashioned way, using a chain and elastomeric springs to bring impacted teeth into position. This tiring process requires repeat visits, provides inconsistent tooth pressure, and delivers less comfort and convenience for the patitent. Dr. Coleman’s solution sought to use the superelastic properties of Nitinol alloy to address all these shortcomings if only we could find a way to form and secure the exotic metal.
What is “Superelasticity”?
Nitinol is a unique alloy of Nickel and Titanium- besides its ability to maintain a “memory” which can be restored thermally, when used as a spring it can be extended well beyond the permanent deformation of conventional steel and other common alloy metals and still maintain its initial force specification. Grant recognized that this property could potentially allow a short spring to reach all the way from arch wire via surgery to an impacted tooth and provide a consistent force to move the tooth all the way into its proper position. This yields a substantially improved experience from multiple perspectives.
The challenge was to design appliance features that would align with practical methods and processes to secure this exotic material and also scale for production and distribution.
Where do you Start?
As with most projects we started with a consultation and benchmarking other similar products documenting their features & benefits and understanding what new benefits Grant’s new idea could provide. Grant shared images that helped him describe the problem of impacted teeth, which helped understand how a Nitinol spring can save time, cost, and provide a better solution for both doctor and patient.
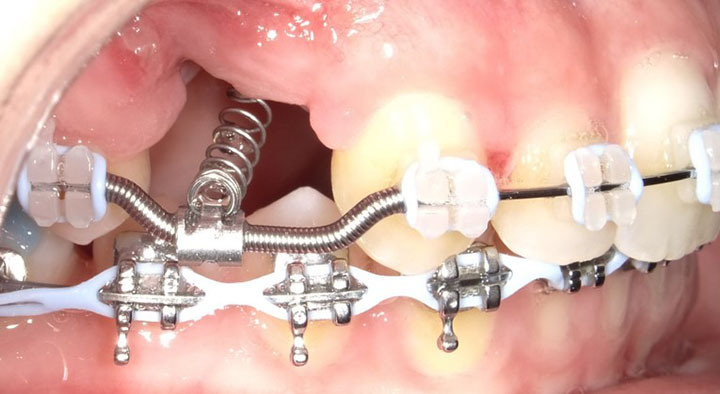
Following that, we got to work identifying compatibile processes with Nitinol and learning about the limitations and opportunities provided. Our intial prototype identified a vendor who could supply etched stainless anchor pads (that attach to the tooth during surgery). These pads were stamped and processed components that could be readily manufactured and delivered to spec. The bonding side of these anchors included a spot welded mesh to improve tooth bond and reduce the risk of a pad coming loose and requiring a surgical correction.
How can we make this?
Conversations with that manufacturer led to some adaptations of his design to include both a welded on bracket and a bent tab that could thread a spring onto it.
As the anchor would necessarily be subdermal in most initial use cases, our overall size needed to be minimal while remaining secure. To that end, we proposed a notched bracket with welded stainless tube. This allowed for a straightened piece of nitinol spring to thread through that loop and a laser weld to create a ball at the end of the wire.
Nitinol springs are typically manufactured in a continuous helical length and then cut to size.
Therefore this would require a specialized tool to take a helical spring and straighten a short section for installation. This was accomplished electrically by modifying an existing wire stripper with an electrically conductive “blade” feature. The tool inserted metal blades into the helix and then stretched the helix straight. To set the new straight metal section an electrical current was sent through the blades to heat the wire section between the contact points. This yielded a tight and accurate spring with a straightened end for installation.
A laser welding contractor in California was met with and recruited to ball the end of the wire once inserted into the bracket anchors. This design yielded a compact but reliable solution, but after some considerations we moved to a larger threaded design to help streamline the process and keep manufacturing more consolidated.
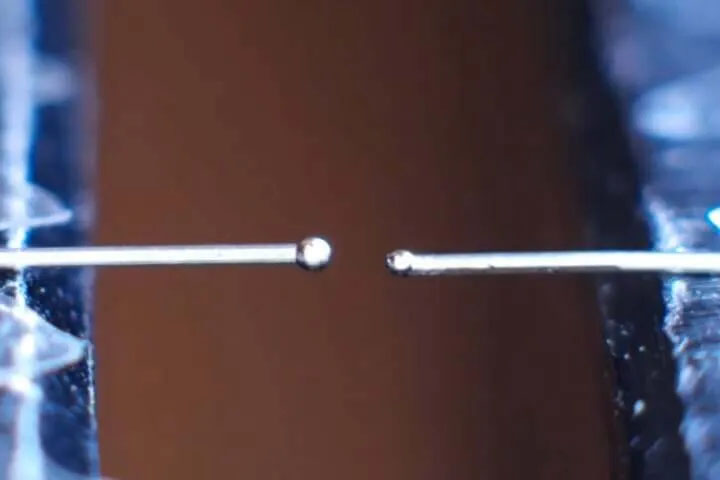
The version that was eventually commercialized simply threads a full nitinol helix onto both the bonded tooth mount and the archwire anchor. This commecially successful iteration has sold/shipped to 49 of the 50 US states (South Dakota is still a holdout) and over 20 foreign countries, as well as 3 branches of the US military. It’s been featured in an article in the Journal of Clinical Orthodontics and is presently helping patients around the world.
For more information please visit the “IsoGlide Website” linked here.